Sam O’Gorman asserts that a worker from a 1920s building site would not be all that shocked by what they saw if they were transferred to a modern project.
“In general, construction in Europe and the US continues to be done primarily by hand – not all that different from how it would have been done a century ago,” states Mr Gorman, an associate partner in McKinsey’s property team.
The McKinsey Global Institute came to the conclusion back in 2017 that the construction sector could increase productivity by 50–60% and increase the sector’s global value by $1.6 trillion (£1.3 trillion) annually.
Since then, efficiency has increased thanks to better manufacturing procedures and the usage of new software and apps, but not as much as one may have thought, according to McKinsey.
When it comes to digitalization, the construction industry lags behind many other sectors. Digital adoption in the broadest sense has been sluggish, according to Mr. O’Gorman.
Several technologies have been hailed as having the ability to completely change the industry in recent years. Among these is 3D printing, which entails extruding materials such as concrete to construct a home’s walls.
One such project being worked on by the University of Maine is creating the largest 3D printer in the world.
The printer created a 600 square foot (180 square metre) home out of a mixture of wood fibres and plant-based resin.
“We are focusing on printing a neighbourhood with nine of these homes because the first prototype home, BioHome3D, has performed incredibly well through two Maine winters,” says Dr. Habib Dagher, executive director of the University of Maine’s Advanced Structures and Composites Centre.
Still, 3D printing houses is still more of a demonstration exercise than a workable idea. Inexpensive, with walls that are often very thick, 3D printed dwellings are challenging to build on any surface other than a level, open area.
Even though there have been several highly publicised 3D-printed construction projects, very few homes have really been constructed in this manner.
According to Mr O’Gorman and Dr. Dagher, modular construction is an additional technology that could improve the efficiency of constructing.
It entails producing the building’s components in a factory, moving them to the location, and then lifting them into position.
“I’m positive that this is the future because of how much better the construction is done. There are a lot of small mistakes made on building sites, according to Dr Dagher.
“It’s preferable to be able to accomplish more in a factory. Both the final quality and quality control are obviously far better. But according to Neil Jefferson, managing director of the UK Home Builders Federation, this technology has also failed to catch on. The problem with manufacturing housing is that you book your stuff in the factory to build those homes, and the materials arrive and you need to stick to the plan,” according to him.
However, due to the government’s current approach to planning policy, there are now many delays in projects in this country. And it just isn’t effective; a more adaptable strategy is required.”
Developers frequently have to modify designs as a project progresses due to changes in the market, and they require a certain level of assurance that they will be able to sell their homes fast once finished. This can be a concern for individual developers, but it is less of an issue for projects for housing associations or local authorities.
Automated Architecture, or AUAR, located in Bristol, is one business hoping to avoid some of these issues. It intends to licence micro-factories to utilise robots to construct wooden buildings. These micro-factories will construct up to six-story structures that are put together on-site or at the factory from conventional parts.
Larger construction companies are supposed to be able to licence a microfactory for an initial outlay of about £250,000 plus a monthly fee after that.
“AUAR’s partners don’t need to invest millions in setting up large factories, as modular housing companies do, but can immediately offer innovative, high quality, low-energy homes at market rates to their customers,” explains Mollie Claypool, co-founder and chief executive officer.
She claims that automation lowers risk and waste, speeds up build times, and increases developer margins. According to her, labour expenses might be 20% to 60% less per project when using this strategy than when using standard building techniques.
According to her, the company has four customers signed up now and plans to build over 30,000 energy-efficient homes year, with the goal of increasing that number to 140 by 2030. Many of the smaller, less noticeable aspects of the home construction process are becoming digitalized.
Even though the sector hasn’t undergone the same kind of significant change as other industries. As it’s largely analogue and hasn’t altered much, the actual construction portion receives the greatest attention and headlines. “The rest of the chain is actually digitising pretty nicely if you look at it,” Mr. O’Gorman says.
“Digital technologies are being used by people to locate land, and artificial intelligence is being used to anticipate future values using a wide range of indicators. Over the past ten years, the design process has become increasingly computerised.
According to Karoliina Torttila, director of AI at industrial technology company Trimble, these kinds of back-end enhancements are probably going to have the biggest impact on streamlining the house-building process
Such actionable data not only encourages communication between teams on the construction and back office operations, but also informs forecasting, planning, and purchasing decisions,” she states.This helps create a smoother process – even if the industry remains fragmented.”
Group Media Publication
Construction, Infrastructure and Mining
General News Platforms – IHTLive.com
Entertainment News Platforms – https://anyflix.in/
Legal and Laws News Platforms – https://legalmatters.in/
Podcast Platforms – https://anyfm.in/
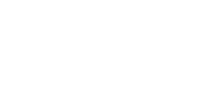