The use of fibers to reinforce concrete materials is a well-known concept. It has been there since ancient times, with rice straw mixed with mud bricks and horse hair mixed with mortar. However, in our modern construction practice, we have forgotten the ancient practice of controlling concrete cracks. It is normal for concrete to crack. Portland cement concrete is considered to be a relatively brittle material, which is prone to cracking during the plasticity and hardening stages.
Plastic shrinkage occurs when the evaporation of water on the surface of concrete is greater than the rising amount of bleeding. Since the tension of concrete in the plastic phase is very weak, volume changes can cause surface cracking. As it hardens, the water in the concrete pores begins to evaporate. This causes the concrete to shrink due to volume changes and is constrained Cracks can lead to negative perceptions of quality, durability, and suitability, but in most cases, they only become aesthetic issues.
Cracks can also cause disputes between owners, architects, design engineers, and contractors, leading to work delays and increased costs due to work stoppages and evaluations, which are more serious than the actual consequences of cracks. One of the solutions to this problem is to add fibers to the concrete.
The use of fibers helps to improve the performance of concrete in the plastic and hardening stages, thereby making the concrete more durable. The addition of synthetic fibers helps reduce thermal cracks and shrinkage cracks. The addition of steel fiber improves the ductility, post-crack tensile strength, fatigue strength and impact strength of the concrete structure. What is fiber reinforced concrete.
FRC is Portland cement concrete reinforced with more or less randomly distributed fibers. In FRC, thousands of small fibers are randomly dispersed in the concrete during the mixing process, thereby improving the performance of the concrete in all directions. Fiber helps to improve pre-crack tensile strength, post-peak ductility, fatigue strength, impact strength, and minimize thermal cracks and shrinkage cracks.
A variety of fibers are used in concrete. For each application, it is necessary to determine which type of fiber best meets the specific application. The different types of fibers used as concrete reinforcements are synthetic fibers and steel fibers. The different types of synthetic fibers used are polypropylene, nylon, polyethylene, polyester and glass fibers
For construction and decorative concrete products and to prevent early cracking, synthetic fibers can be used. Steel fiber is used in applications where concrete properties must be improved during the hardening stage, that is, the post-crack flexural strength, abrasion resistance, impact resistance and crush resistance of the concrete.
The early volume changes of concrete can cause weak planes and lead to the formation of cracks, because the stress generated in the concrete body at a certain time exceeds its tensile strength. The mechanical blocking effect of synthetic fibers and steel fibers inhibits the growth of these micro-shrinkage cracks. The internal support system of the fiber suppresses the formation of plastic settlement cracks.
The uniform distribution of the fibers throughout the concrete prevents the formation of large capillaries caused by the migration of water to the surface. concrete and their evaluation is ACI Journal of Materials, May-June 1994, Vol. 91, No. 3, pp. 280-288. “Fiber’s contribution to the reduction of cracks in cement composites during the initial and final setting periods”

The main variables investigated are: fiber type, matrix composition and test method. The fiber type is composed of synthetic fibers. The length of synthetic fibers ranges from 1 to 60 mm, the volume content is 0.9 kg/m3, and three lengths of steel fibers. 30, 50 and 60mm were studied at volume contents of 45 and 60 kg/m3. Synthetic fibers are made of nylon, polyethylene, polypropylene and polyester.
In the case of the test method, the main variables are the thickness of the specimen and the plane size of the test board. The results show that both steel fibers and synthetic fibers have made a clear contribution to reducing shrinkage cracks during the initial setting and final setting.
News Source : NBM&CW
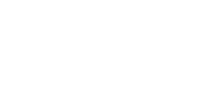