%20(1).jpg)
Joseph Worland, associate director at Lloyds Banking Group; Stephen Wightman, regional director and UK MMC lead at Faithful + Gould; Jessie Wilde, deputy project director at Bristol Housing Festival; Edward Jezeph, senior investments manager at Homes England; and Pablo Martinez Rodriguez, senior lecturer at the Department of Mechanical & Construction, were among the industry experts I spoke with to discuss the merits of MMC and how it can break into the UK construction market.
Standardization of MMC can be a double-edged sword, according to Pablo Martinez Rodriguez of Northumbria University: “Standardization can help the industry grow, but it can also suppress innovation.”
What matters, he said, is who sets the standards. Jessie Wilde of the Bristol Housing Festival agreed, saying that standardisation should be developed in collaboration with supply chains.
We need to be clear about what we’re looking for MMC to provide, according to Stephen Wightman of Faithful + Gould, in order to determine whether or not it’s succeeded: “Standardizing components isn’t always the best solution. We need to standardise performance criteria so that users can get the results they want. MMC, for example, provides far better acoustic attenuation between room spaces than traditional construction methods. Traditional builders would have to add content to increase building performance to close the gap with what MMC already provides if performance standards included this type of acoustic attenuation as a performance criterion.”
MMC often outperforms traditional construction methods in terms of both speed of delivery and building fabric quality, according to Wightman. “Set performance standards, and the industry will innovate,” he continued, “much like the car industry did when it was given emissions targets.”
“We do need confidence in the building technologies we’re using,” Homes England’s Edward Jezeph added, “but we can get that by looking at existing warranties and insurance markets.”
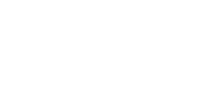