The combination of geopolymer technology and 3D printing is transforming the construction industry, offering sustainable and efficient construction methods. This innovative approach combines the speed and flexibility of 3D printing with the environmental and structural benefits of geopolymer concrete. 3D printing, a technology revolutionizing industries like healthcare.
Automotive, fashion, and food, is transforming the construction sector. It allows for design complexities and faster construction, introducing a new paradigm. 3D printing technology, using materials like concrete, plastic, and metal, addresses sustainability, safety, and affordability.traction, allowing for precise material use, less on-site waste, traction, allowing for precise material use, less on-site waste, traction, allowing for precise material use, less needs.
Geopolymer technology, derived from minerals and industrial waste, is gaining popularity in the construction industry as an environmentally friendly alternative to traditional Portland cement. This technology reduces the industry’s carbon footprint and offers superior thermal resistance strength. Recent advancements in geopolymer technology also demonstrate compatibility with 3D printing.
The success of 3D printing in concrete depends on several factors, including workability, viscosity, setting time, strength, and compatibility with 3D printing technology. The primary material used in 3D printing is Geopolymer Concrete (GPC), which is formed by activating a mixture of fly ash, slag, or other pozzolanic materials with alkaline solutions. Fine aggregates like sand are added to improve workability, flowability, and mechanical properties.
Superplasticizers are incorporated to enhance fluidity, prevent nozzle clogging, and improve layer adhesion. Alkaline activators like sodium hydroxide or potassium hydroxide initiate geopolymerization reactions, influencing setting time and strength development. The material specifications for content of 600-800 kg/m³, alkaline solution content of 140-180 kg/m³, and aggregates (sand) comprising 58-67% by weight of the total mix.
The combination of geopolymer technology and 3D printing has shown promising results in various projects worldwide. For instance, COBOD and Kamp C in Belgium successfully 3D printed a two-story house using geopolymer concrete, showcasing the feasibility of 3D printed construction and its speed and cost advantages. Initiatives like Project Milestone in the demonstrated the versatility and creativity of 3D printing.
In the global South, organizations like ICON are working to create affordable, resilient, and quick-to-build 3D printed homes using a specially designed 3D printer called Vulcan. In India, TVASTA has been at the forefront of applying 3D printing technology in the construction sector, building India’s first 3D printed house in just 21 days using ‘Concrete 3D Printing’.
This approach allows for greater architectural customization, efficient material use, and significant waste reduction. TVASTA also partnered with Godrej Construction to create 3D printed bus stops in Mumbai, showcasing the potential of 3D printing in transforming construction practices. However, challenges TO persist, such as the development of building.
Harnessing the Potential of 3D Printing with Geopolymer Technology
The fusion of 3D printing and geopolymer technology is revolutionizing construction and manufacturing. Geopolymers, eco-friendly alternatives to traditional cement, offer superior strength, thermal resistance, and reduced carbon emissions. When combined with 3D printing, they enable rapid, cost-effective, and sustainable production of complex structures.
This innovation is particularly transformative in construction, where 3D-printed geopolymer concrete can create resilient, durable buildings with minimal waste. Unlike conventional concrete, geopolymers do not rely on carbon-intensive Portland cement, significantly reducing environmental impact. Additionally, their high heat and chemical resistance make them ideal for applications in aerospace, automotive, and infrastructure sectors.
The adaptability of 3D printing allows for intricate, customizable designs that would be difficult or expensive to achieve using traditional methods. This opens new possibilities in architectural freedom, disaster-resistant housing, and space exploration, where geopolymer-based structures could support extraterrestrial habitats.
Group Media Publication
Construction, Infrastructure and Mining
General News Platforms – IHTLive.com
Entertainment News Platforms – https://anyflix.in/
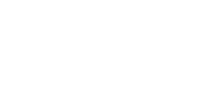