Following a temporary hiatus brought on by the epidemic, India’s construction industry is expected to rise to become the third largest in the world, behind only the United States, China, and Japan. The majority of the country’s 2030 housing stock is yet unbuilt.
The construction industry is widely regarded as resource-intensive, contributing 40% of global carbon emissions because of its extensive reliance on polluting activities including mining, transportation, and the production of building materials.
According to Union government estimates from 2019, India has a 25% share of carbon emissions, but its rate of resource extraction is almost four times higher than the worldwide average—at 1,580 tonnes per acre, compared to 450 tonnes per acre for the rest of the world.
Given this, many experts think that there should be a strong push towards sustainability, particularly in light of India’s commitment to achieve net zero emissions by 2070, which was announced at the United Nations Framework Convention on Climate Change (COP26) in November 2021.
Thus, sustainability concepts must be used to every aspect of building, from the initial design to the final demolition and local material procurement, according to Sarah Khan, senior associate at the Centre for Study of Science, Technology, and Policy think tank.
The building industry must to tackle decarbonisation at several levels, including material manufacturing, transportation, and site management, according to Shashank Bishnoi, an IIT Delhi civil engineering professor.
Transcending traditional material
Cement and steel, two essential components of traditional Indian building, are both high in carbon. The impact on the environment is too great to be disregarded due to the enormous magnitude. The most common substance manufactured worldwide is concrete. Concrete makes up more than half of what we create, according to Bishnoi.
He is a member of a research team that has created limestone calcined clay cement, or LC3, a low-carbon cement that, when compared to the majority of commonly used conventional cement (ordinary Portland cement, or OPC), may potentially lower emissions by 40%.
In India, this cement has been used in over 25 different projects. Notably, this cement was used in November 2019 to construct the Swiss Agency for Development and Cooperation building located within the Swiss Embassy complex in Delhi. Its usage has expanded both domestically and internationally in 2023 after receiving certification from the Bureau of Standards (BSI).
Climate change and circular economy specialist Vaibhav Rathi stated that red clay bricks, another common building material in India, is carbon intensive and should be avoided, much like steel and cement. High temperatures in kilns are necessary for the creation of red clay bricks, which uses a lot of energy. Emissions of greenhouse gases result from the burning of fossil fuels to provide this energy. In addition, he noted, clay extraction disrupts regional ecosystems and causes habitat degradation, soil erosion, and biodiversity loss.
Rathi claims that fly ash bricks, which are produced from the refuse of coal-fired power plants, are a much greener option that are now on the market and ought to be used instead of other building materials. Even though the union power ministry has ordered the free distribution of fly ash to brick makers within a 300-kilometer radius of power plants, he said that Bihar has taken proactive measures to ensure their acceptance. However, only 64% of the fly ash produced by coal power stations was utilised by the sector, according to the Central Electricity Commission (CEC).
Increasing the use of industrial and construction and demolition (C&D) waste is another strategy that experts recommend to lessen environmental stress in the industry. Aluminium and other metals that are typically utilised in Although there is a viable secondary market for construction, despite the Union government’s notification of the C&D Waste Management Rules, 2016, demolition debris is frequently left unused.
Concrete can be made using C&D waste as aggregates, according to Rathi. There are no rules requiring the use of recycled materials in building, despite the fact that BIS permits the use of 25% of them, which is a cost-effective practice.
According to him, only major builders use this strategy because states reward it and it’s one of the requirements for buildings to be certified green.
In Uttar Pradesh, for instance, structures that receive a four-star rating from Teri’s Green Rating for Integrated Habitat Assessment (GRIHA) system are granted a 25% increase in floor space ratio.
States like Delhi, Chhattisgarh, West Bengal, and Rajasthan offer similar incentives in relation to greater FSI (Floor Space Index, or maximum allowable floor area relative to the site size).
According to Mala Singh, co-chair of the Confederation of Indian Industries-Indian Green Building Council (CII-IGBC), the top 1,000 Indian companies are required by Sebi to publish ESG disclosures, which inadvertently promotes green growth.
Furthermore, she claimed, environmental approval for structures obtaining green certificates is expedited by the Union Environment Ministry. Compared to just 20,000 square feet in 2003, “these have led to 11 billion square feet of real estate getting IGBC certifications today,” the speaker stated.
Green tactics take time to get traction.
The building industry’s increased awareness of green strategies has led to changes in the materials sector, with over 8,000 CII-certified eco-label construction materials easily accessible on the market.
State notification and enforcement of Union government standards, such as the Energy Conservation Building Code (ECBC) for all big commercial, non-residential structures and the Eco-Niwas Samhita (ECBC-R) for residential buildings, has lagged, however, when it comes to mandates.
Although these laws have been accepted by 24 states, more rigour needs to be used by state and local authorities in order to implement them, according to a January 2024 World Resources Institute research.
According to Vivek Anand, lead architect at Rudrabhishek Enterprises, a consulting firm handling a number of projects for the Union Ministry of Housing and Urban Affairs (MoHUA), more work has to be done to raise awareness of the lower life-cycle costs and other advantages of sustainable construction in order to encourage smaller developers to adopt it. In order to encourage broader adoption, he promoted rewarding sustainable methods with certification, tax breaks, or other financial aid.
A minimum 3-star GRIHA rating has been implemented for the construction of all government buildings since August 2016 by the Central Public Works Department (CPWD), a division of MoHUA that is in charge of managing the construction of central government structures. An additional set of green standards will be accepted by the body in the upcoming months, according to a CPWD representative.
Inadequate dust control techniques and C&D waste storage within facilities also contribute to pollution. Waste that is required to be processed separately—C&D waste—ends up mixed up with municipal rubbish and dumped in landfills. However, dusty surroundings surround the building site due to inappropriate storage of sand and cement.
However, Manit Rastogi, the founding partner of the architecture and urban design firm Morphogenesis and a founding member of the GRIHA Council, noted that there are additional opportunities to reduce dust and waste if more modern technologies like prefabrication, modular construction, and 3D printing are adopted.
The Cambridge Layout post office in Bengaluru, which is the first 3D-printed public building in India, was constructed by L&T in the middle of 2023 following the Building Materials and Technology Promotion Council (BMTPC), an autonomous agency under MoHUA.
According to BMTPC Executive Director Shailesh Agrawal, the council has launched a number of efforts in recent years to mainstream emerging technology. He mentioned the six 1,000-unit lighthouse projects under the Pradhan Mantri Awas Yojana (PMAY), which exhibited six distinct prefabricated technologies that minimise in-situ dust and pollution.
According to him, BMTPC has been engaged in a number of demonstration projects, constructing 40–50 dwelling units each in Assam, Bihar, Nagaland, and Jammu and Kashmir, among other locations, with the union government covering all project expenses.
But the primary obstacle, according to Agarwal, is still people’s innate preference for conventional materials like cement, concrete, and brick. “We had observed bamboo being used in the northern states, and it is widely known in the industry about their sustainability characteristics, but there is no real demand in the market,” he said.
Group Media Publication
Construction, Infrastructure and Mining
General News Platforms – IHTLive.com
Entertainment News Platforms – https://anyflix.in/
Legal and Laws News Platforms – https://legalmatters.in/
Podcast Platforms – https://anyfm.in/
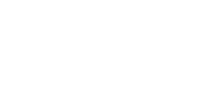