Strabag AG implements complex construction projects, especially in the development of tunnels and infrastructure, and has representative offices in approximately 30 countries around the world. Since 2011, it has been active in the field of building construction, civil engineering, tunneling and professional foundation engineering in the UK.
For tunnel construction projects, Strabag relies on machines from Progress Maschinen & Automation. For a project in North Yorkshire, Strabag built a prefab plant on the construction site and ordered an M-System BlueMesh® welding equipment with mesh rolls, a Tunnel Master trapezoidal welding machine and an EBA S16 automatic hoop Rib bending machine.
In the middle of the North York Moors National Park in northeastern England, a 37-kilometer transport tunnel system is being constructed. The Strabag North Yorkshire polyhalite project is part of the Woodsmith project and is owned by Anglo American, one of the world’s largest.
mining companies. This is to extract minerals from the largest polyhalite deposit in the world, which is a mineral used to produce fertilizers. Of the 2.66 billion tons of polyhalite deposits, 280 million tons are located within 5 kilometers of the proposed mine. This only accounts for 7% of the project’s specified resource area.
The rapidly growing and urbanized world population constantly needs more fertilizers to produce food. Polyhalite is extracted from a depth of 1.5 kilometers through a mine, and transported underground by the MTS (Mineral Transportation System) to the processing hall in Teesside for processing.
The processed products are shipped to ports and mainly exported overseas. The biggest challenge in tunnel construction is safety precautions and evacuation strategies. Over time, high security standards, tight schedules, historical funding issues, and contract changes have added challenges to the project. Close cooperation with the on-site customer team makes it possible to achieve the best results.
From the design stage, the project focused on sustainable and environmentally friendly construction methods. MTS itself is environmentally friendly to the mine, and there is no need to use roads or other ground transportation tools. The prefabricated factory built close to the site also fits this concept.
The sustainable procurement policy guides the way in which raw materials are supplied. It was decided very early to purchase sand and aggregates from local quarries, and specially selected transportation routes so as not to disturb the tranquility of the national park. Modern diesel-electric hybrid tunnel locomotives use kinetic energy recovery to maximize the use of the steep section and length of the tunnel, radically reduce emissions, and minimize ventilation requirements.
News Source : NBM&CW
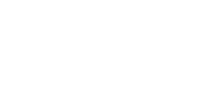